Location:Home > News > Industry NewsNews Center
CHINESE CONTAINER BUSINESS SETS ITS SIGHTS ON MODULAR
Author:未知 Source:0 Updated:2018-11-27 15:11:24
A RECENT VISIT TO CIMC (CHINA INTERNATIONAL MARINE CONTAINER GROUP) AFFORDED JAMES MARSDEN OF TSA MANAGEMENT A FIRST-HAND LOOK AT MODULE PRODUCTION IN CHINA. HERE, HE SHARES HIS INSIGHTS.
Driving through the gates of the CI
A RECENT VISIT TO CIMC (CHINA INTERNATIONAL MARINE CONTAINER GROUP) AFFORDED JAMES MARSDEN OF TSA MANAGEMENT A FIRST-HAND LOOK AT MODULE PRODUCTION IN CHINA. HERE, HE SHARES HIS INSIGHTS.
Driving through the gates of the CIMC (China International Marine Container (Group) Ltd.) Jiangmen City manufacturing base in Guangdong province China, walls of shipping containers stacked either side loom skywards, a reminder of a commercial legacy that is now being adroitly repurposed to produce modular construction solutions.
The primary purpose of my visit was to see first-hand the capabilities of the CIMC Modular Building Systems (CIMC MBS) manufacturing base. CIMC MBS was set up in 2004, leveraging its well-developed shipping container technology and applying it to volumetric modular building systems. The Jiangmen City base comes complete with its own port, guaranteeing traffic-free access to the larger ports of Shenzhen and Hong Kong.
The Australian arm of CIMC MBS was established in 2008, setting up in Perth off the back of the mining workforce accommodation demand. With demand in this sector dwindling, there is now a focused shift towards hotels, student accommodation and aged care; essentially any sector characterised by a high degree of repetition.
Whilst delivery experience across these sectors in Australia remains limited – three completed projects and two in development – in the UK, CIMC MBS has completed over 20 projects equating to approximately 2000 modules, typically across the hotel and student accommodation sectors for clients including leading global hotel brands. One of its quickest programs was delivered for a major UK hotel project, 39 weeks from commencing documentation to achieving practical completion.
Stepping into the MBS factories, the Jiangmen City base is not unlike similar facilities in Australia, with one obvious difference; scale. At full capacity, it is understood the plant is able to produce 400 modules per month. In the case of a hotel or an aged care facility, this equates to 800 beds.
“Stepping into the MBS factories, the Jiangmen City base is not unlike similar facilities in Australia, with one obvious difference; scale. At full capacity, it is understood the plant is able to produce 400 modules per month. In the case of a hotel or an aged care facility, this equates to 800 beds.” James Marsden, Associate Director, TSA Management.
In an obvious segue from CIMC’s core business, module structure is based on shipping container technology. Custom size modules are available, however this will typically be governed by logistics at the destination. Irregular module shapes are no problem, although more welds introduce increased labour and time, a fact which needs consideration in terms of cost and degree of repetition.
Fit-out delivery is characterised by a long production line. Any materials may be used, provided they can be delivered to the CIMC MBS base. Careful consideration needs to be given to supply and lead times of materials, particularly if it is not a regular supplier to CIMC MBS. Corridors are typically finished raw with finish strips completed on site between modules, with a similar approach taken for facade treatments.
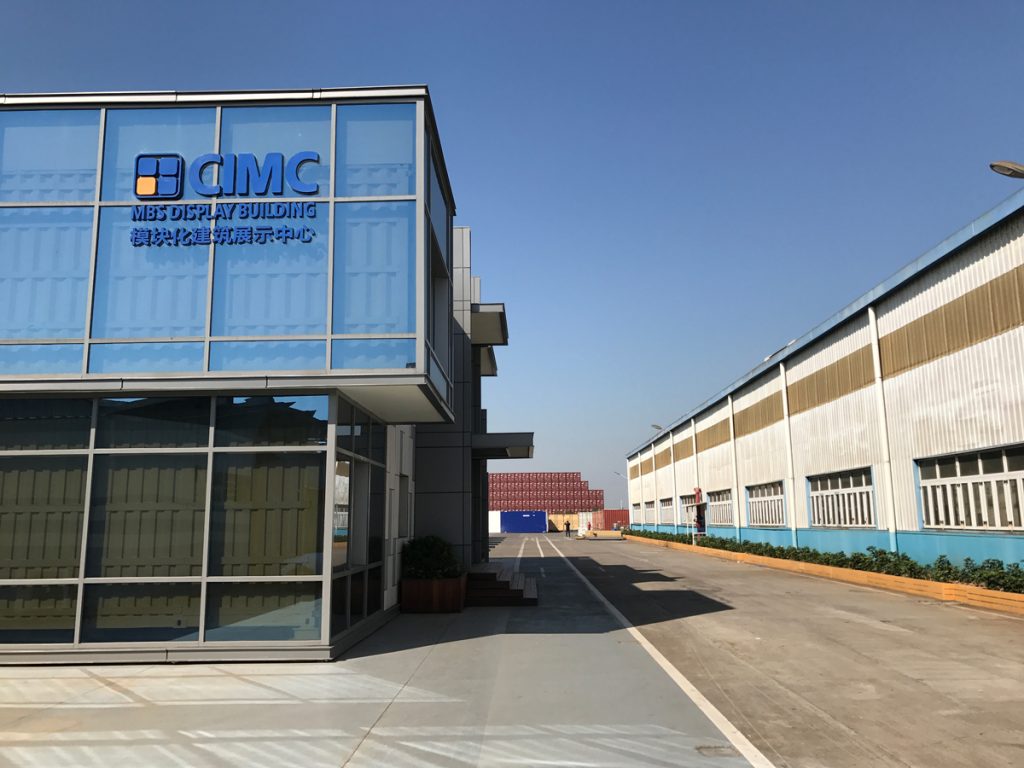
A completed module can make its way from port to site in a little less than four weeks, assuming an Australian east coast location. CIMC MBS take full responsibility for the modules delivered to site. Under a supply only arrangement, sequencing and installation rests with the local contractor. Support is still available however, with guidance and assistance provided by CIMC MBS: an installation guide, typical details for all connections, colour coding and numbering – think IKEA or Lego.
I haven’t experienced a completed CIMC MBS project, but the on-site prototype gave a sense of what’s possible. It comprised 12 modules over two floors, primarily set up with hotels and residential units in mind, with a range of room layouts, also incorporating an internal stair case. Wandering through the prototype, any persistence of social stigma typically associated with modular builds quickly disappears. The level of quality certainly met expectations.
“I haven’t experienced a completed CIMC MBS project, but the on-site prototype gave a sense of what’s possible. It comprised 12 modules over two floors, primarily set up with hotels and residential units in mind, with a range of room layouts, also incorporating an internal stair case. Wandering through the prototype, any persistence of social stigma typically associated with modular builds quickly disappears. The level of quality certainly met expectations.” James Marsden, Associate Director, TSA Management.
I suspect the quality control for the prototype of a new project would need to be monitored closely to set the benchmark for the remaining modules. In corridors and stairs, any joins between the modules were invisible, demonstrating the precision of the pre-manufactured approach. When it came to human perception of accelerations, I did notice the corridor floor on ground level to have a small bounce in the mid-span of modules. For the prototype, I am not sure of the specification for human comfort relating to vibration, however I would suggest this would need due consideration through the design phase.
The capability and capacity of CIMC MBS are impressive, particularly when supported by the logistics network of parent company CIMC. There is a willingness to make this work in the context of the Australian built environment, and I am sure it will only be a matter of time before we start to see an increased supply of modules to Australian shores. In addition, my visit to CIMC MBS also reinforced the view that a collaborative approach, embraced from the outset by the entire project team, is key to the success of any off-site manufactured project.
James Marsden is an Associate Director with Australian company TSA Management, which specialises in providing independent project based services to private sector and government clients. The CIMC MBS visit formed part of a wider research project reviewing national and international practices of off-site construction methodologies and its impact on project procurement in the context of the Australian built environment. James may be contacted at james.marsden@tsamanagement.com.au for further information regarding this project and his CIMC MBS visit.
source from:http://builtoffsite.com.au/issue-09/chinese-container-business-sets-sights-modular/